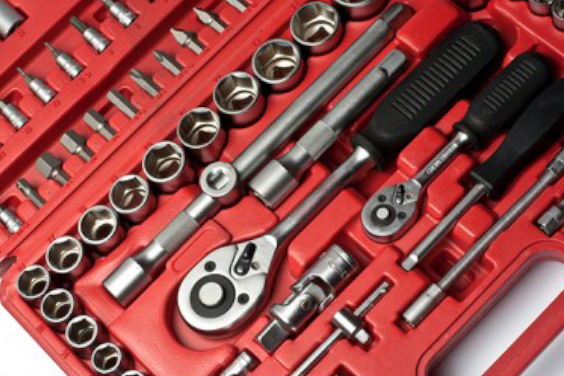
Insert Molding Process Step by Step
It is dangerous to make use of components after they’ve been manufactured without encasing them with plastic. It’s essential to encase these components to make
Share
Share
For the whole period that injection molding has been around, the manufacturing process has received a huge boost. Injection molding is not only fast but is very cost-effective, where mass production and repeatability are valued. Most of the plastic items we use on a daily basis are made using injection molding.
We are going to explore how a plastic injection mold is made, the types of applications the process can be used for, and the benefits it brings to the table. If you have been thinking of getting into the plastic molding business, then this could help you know what’s required.
Source: Pinterest
This is a hollow metal block that is designed with cavities that are used to give shape to molten plastics through the process of injection. It is the metallic cast that holds and gives shape to molten raw materials until they cool down and take shape. A plastic injection mold has the following parts that are necessary for its functionality to be assured.
Guide Pins: These are pins that are used to locate the core and cavity of the injection mold to ensure that the entire structure matches perfectly to avoid misalignment that would lead to deformed products. It is usually installed in one half of the mold and fits into holes drilled into the other half for a secure fit.
Runner: This is a section of the mold that connects the molding cavities to the sprue bush to provide a clean passageway for the molten raw materials to pass through unhindered. It usually comes in round or trapezoid shape.
Gate: This is a narrow part of the runner that determines and controls what goes into the mold and what doesn’t. Gates come in varying shapes and designs, but they all serve the function of controlling the flow of molten material into the mold. Once the right amount of materials is injected into the mold, the gate is closed.
Sprue: Also called the Bush, this is a tapered hole that’s found smack in the center of the mold, and it is the point where the flow material travels to the runners from the injection nozzles.
Locating Ring: This is a round ring-like structure that helps the injection nozzle line up with the center of the mold to direct the molten materials so that they can spread evenly across.
Mold Cavity: This is the entire empty space within the mold that holds the molten materials in place until the cooling process is complete. The size of the final product is determined by the size of the mold cavity.
Ejector Pins: These are pins that are located under the mold that is used to push the molded product once it has cooled down out of the mold cavity to create space for another injection. It has to be strong enough to deal with sticky products.
Injection molds are a very important part of the entire process as they determine the shape and design of the final product. Any slight defect that is made in them will be reflected in every single product that’s made through it. The following are the ways through which an injection mold is designed and created.
Source: Pinterest
CNC Machining is a heavy-duty process that uses a set of hard tools to burrow and drill holes into metal blocks through automated guidance to fashion out molds that are then used in injection molding processes.
A conventional CNC Machine comprises a robotic arm that is loaded with all kinds of tools used for cutting and drilling holes. Thanks to advanced technologies, the injection molding process has become even more accurate and precise, and it can be used to create some of the best molds you will ever come across.
Everything about the mold design, from the shape to the dimensions, is defined by the CNS machine. It figures out the right measurements based on the data that’s fed into it, and it then translates these instructions into tangible data that is then used to map out and cut out the mold from the metal block with the highest precision.
These instructions are translated by a computer-aided Design program (CAD) and then executed by a computer-aided manufacturing software (CAM), and once that has been done, the mold is accurately carved from whatever block is being used as the base material.
Source: Pinterest
Electrical Discharge Machining (EDM) is a process that attains the desired shape from a base material using an electrode that is coated with graphite or copper. This electrode is mounted on the EDM machine and placed over the base workpiece that is then dipped inside a dielectric fluid.
Once the electrode is lowered into the fluid, it begins destroying and dispersing all the metal that is opposite to the electrode with the help of a controlled electrical source. At no point does the electrode come into contact with the workpiece; there’s always a spark gap that’s about a thousandth of an inch minimum that’s maintained between the two.
The electrode continues chipping away the unwanted parts in a slow manner until what’s left is a finished injection mold ready for use. This is a much slower process compared to CNC Machining, and it also consumes a lot of energy. However, it is preferred due to the fact that it can be used to create shapes that are too complicated for CNC Machining.
Another great advantage is that a mold made using the EDM process doesn’t require any extra heat-treatment since the EDM process handles all the parts, and this includes treating the workpiece. All that would be needed afterward are some polishing, and the mold would be ready for use.
Source: Pinterest
There’s a lot of heat involved in injection molding, and the best way to ensure that every item that is made comes outright is to have a reliable mold that can handle high and low temperatures without affecting the shape of the final product. The following are the advantages of using a metallic mold for plastic injection.
They are durable and can be used for a very long time. Molds made out of aluminum or steel are very sturdy and can take a considerable amount of beating before they start malfunctioning. This could be many years later, allowing you enough time to make the most out of them.
They can handle high and low temperatures, and this makes it easy to design any shape without deformities popping up. The raw materials being injected into the crates usually come in very hot, and if the molds have a low melting point, they may end up melting in the process, contaminating the entire batch.
The development times are way faster, especially the cooling part. This is due to the fact that metals are good conductors of heat. Once the molten material has been spread out evenly, the mold can quickly dissipate the heat out to accelerate the cooling process.
The molds can be used repeatedly for long without any changes happening to the overall design. Metals have a high tolerance to the extreme changes of heat and cold, and this is what makes injection molding a reliable process when it comes to mass production of small and big items.
A good and reliable mold will bring down the cost of production, especially if you are dealing with mass production. The repeatability it accords manufacturers means that there is a better utilization of raw materials and the energy consumption goes down as there are no interruptions involved in the process.
Modifications can be made at any time if you want to alter the shape of the design. The mold can be made bigger or smaller depending on your needs, and this flexibility is another added advantage s that makes production more easier and faster. The ability to switch designs without having to start from scratch again is an underrated achievement.
Source: Pinterest
Good as it may be, using molds for plastic injections are not without their limitations. Although the benefits far outweigh the disadvantages, there are some things that you have to be wary of if you do choose to go down this route.
The initial cost of constructing the molds is very high, and the cost can go through the roof if you are planning to run multiple assembly lines. In fact, this mode of manufacturing only makes sense if you are handling large volumes. Dealing with small numbers will only lead to wastage of resources.
There are design restrictions since modifications cannot be huge. Once the mold is set, there’s very little room for flexibility. You can only make limited modifications; the only way you can change the entire design is to make an entirely new mold caret.
Tooling costs are very high. Running a single CNC machine, for instance, can run into thousands of dollars, something that small businesses cannot handle.
Injection molding is an important process in the manufacturing world, and as long as people continue to need plastic products, the industry will continue to grow. When it comes to selecting the right injection mold carte, take your time to research the best materials in order to have a reliable system. For more information, check out our website and have all your questions answered.
It is dangerous to make use of components after they’ve been manufactured without encasing them with plastic. It’s essential to encase these components to make
Transparent plastic is being used in virtually every industry and this is because of its capacity to allow you see through and its ease of
Plastic is a common material used in the production of objects that can be used in homes, the automobile industry, and virtually all sectors. It
Basically, there are two kinds of plastics – thermoplastic, and thermosets. But the majorly talked about kind is the thermoplastic because of its versatile and
+86-755-8524 1121
marketing@rydtooling.com
No. 2, HongKan 1st Road, YanChuan Community, YanLuo Street, BaoAn District, ShenZhen City, China. Post Code 518105.
Subscribe to our newsletter to get manufacturing news and updates!