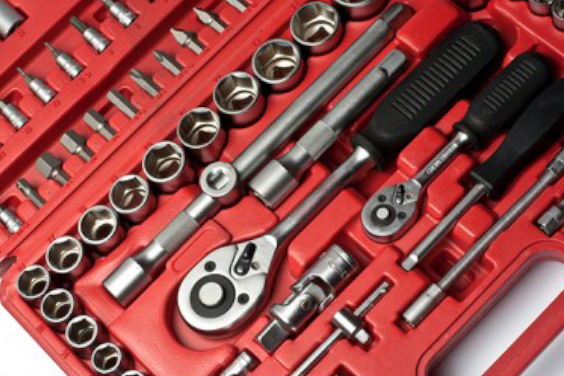
Insert Molding Process Step by Step
It is dangerous to make use of components after they’ve been manufactured without encasing them with plastic. It’s essential to encase these components to make
Share
Share
Injection molding is a complicated process that depends on timing and balance. Getting just one part wrong could end up causing a lot of defections in the final product, rendering the entire process wrong. Among the many defects that products develop is shrinkage. We are going to explore what injection molding shrinkage is, what causes it, the effects it may inflict on the final product, and how to counter it.
Source: Pinterest
Injection molding shrinkage is a defect that occurs when there are contractions in the product being molded due to varying degrees of cooling. The transition from a liquid state to a solidified state can cause some tensions if it is not handled properly. Once the material solidifies, it becomes denser, and if there’s any part that’s still in an aqueous form, the tension becomes uneven, and this leads to the product curving up due to shrinkage. This may seem like a minor plastic defect, but it can cause some serious damage to the final product, and this can make it unusable.
Source: Pinterest
There are about four types of plastic injection molding, each caused under unique conditions; they include the following.
Regional Shrinkage: This is when the rate of contractions varies on the product parts that are between the ones closest to the mold gate and the regions that are nearest to the end of the fill area. This causes the part that’s near the gate to be thicker while the other end to become a little thinner. Therefore, the thinker parts pull in the thinner part, and this causes a warped shrinkage.
Thickness Shrinkage: This shrinkage takes place when the top and the bottom areas of the same mold differ in the rate of cooling. It is a situation where the top part cools faster than the lower part, and this variance causes the mold part to bow towards the cold side, shrinking more and more until that new shape is frozen into place.
Directional Shrinkage: This is a result of a variance in the molecular and fiber alignment. The shrinkage manifests itself parallel and perpendicular to the mold material’s orientation and the direction of flow. The material, therefore, shrinks more in the direction that the flow of the material takes.
In-Plane Shrinkage: It is common for polymers to shrink a little more strongly in the thickness direction than the surface plane. This is caused by a condition called mold restraint which is basically the lack of restraint in the thicker part. This difference in shrinkage causes serious warping from the corners, and it can render the product damaged and unfit for use.
Source: Pixabay
There are many factors that combine to lead to shrinkage in plastic injection molding. Some are completely accidental, and some cannot be avoided completely. The following are some of the causes of this shrinkage.
Cooling Rates: Varying speeds of cooling is the leading cause of shrinkage. When one part starts cooling while the other part is still hot, then the mold will tend to warp in the direction of the already cooling part. To counter this, ensure that the mold crate is well heated before injection and increases the speed of injection molten materials.
Mold Restraints: Once the mold has been injected into the crucible, the likelihood of shrinking in-plane is eliminated, but the threat of shrinking in the direction of the thickness increases exponentially. This is what is called mold restraint. To counter this, ensure that the injection of the material is faster and evenly distributed throughout the mold crate.
Differences in Thickness: Nothing is ever perfect, and there’s a high chance that the mold injection could end up with one part being thicker than the other. The thinner part will most likely cool faster, and this can lead to shrinkage and warping. To counter this, use better injection nozzles that distribute the molten materials evenly.
Temperature Differences: Aside from cooling, if the molten material is injected with huge variations in temperatures, then that will lead to shrinkage because the rate of cooling will not be uniform. The best way to ensure that this doesn’t lead to shrinkage is to maintain a high temperature all through the injection process until everything is evenly distributed in the molding crate with the gates closed.
Plastic Composition: Having different materials melted into the same crucible means that each material will cool at different rates since each of them has different melting and cooling points. This is why many injection molding manufacturers only use the same materials for each batch before switching to another when they are done.
Impurities: Sometimes, impurities may find their way into the mix, and this will bring down or raise the melting and cooling points of the main material. Impurities usually come in the form of additives like glass, ceramic fibers, among others, and since they have a low thermal expansion, they lead to variations in the cooling process. Ensure that the crates are clean every time you want to start a new batch process and avoid adding unnecessary additives.
Molecular Weight: The density of the raw material also plays a big role in determining how bad or how mild the shrinkage will be. Resins that have a high molecular density will have a higher viscosity, and they will take longer to cool down and vice versa. Calibrate the molding crate to accommodate each the density of the raw material that you use.
Defects happen all the time in injection molding, as that is part of every manufacturing process. Minimizing their impact is the best anyone one can do, and there are many tactics you can rely on. To learn more about defects that affect plastic injection molding, visit our website at any time of the day.
It is dangerous to make use of components after they’ve been manufactured without encasing them with plastic. It’s essential to encase these components to make
Transparent plastic is being used in virtually every industry and this is because of its capacity to allow you see through and its ease of
Plastic is a common material used in the production of objects that can be used in homes, the automobile industry, and virtually all sectors. It
Basically, there are two kinds of plastics – thermoplastic, and thermosets. But the majorly talked about kind is the thermoplastic because of its versatile and
+86-755-8524 1121
marketing@rydtooling.com
No. 2, HongKan 1st Road, YanChuan Community, YanLuo Street, BaoAn District, ShenZhen City, China. Post Code 518105.
Subscribe to our newsletter to get manufacturing news and updates!