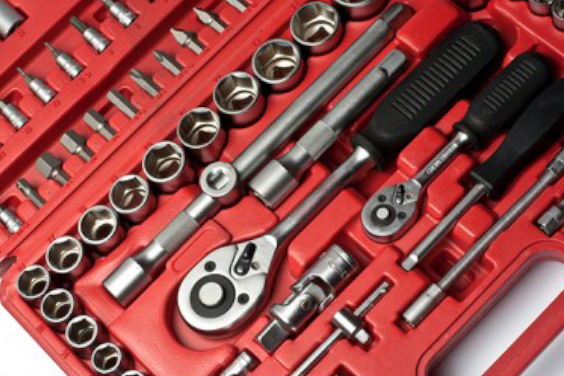
Insert Molding Process Step by Step
It is dangerous to make use of components after they’ve been manufactured without encasing them with plastic. It’s essential to encase these components to make
Share
Share
Plastic is a popular material that may be found in a wide variety of consumer gadgets and medical devices. Because of its versatility and low cost, it is a widely utilized material. Plastic can be finicky due to the high temperatures it must bear to take shape. Because of the difficulties that plastic injection molding poses, it is critical to review the technical specifications for your plastic parts as soon as possible.
Designing plastic injection molded items necessitates a unique set of abilities. It necessitates a thorough understanding of the plastic injection molding process, including how the material reacts and how the injection molding machine operates. There are several things to bear in mind while designing your plastic item, even if you aren’t a plastic injection molding engineer or specialist.
Source: Pinterest
Material should be chosen based on how the object operates, the environment it will be in, and the designer’s preferences. These materials have an impact on how the part feels, looks, and functions. Some are pliable, while others are hard; some are tough, while others are brittle. The The radius The material used will often have a considerable impact on the part’s design.
The material selection procedure might be as simple as looking up the material of an existing part on the market on the internet, or as difficult as determining every single requirement and material attribute from scratch. The first step is to determine the specific requirements for your application. Following that, it’s critical to restrict the options through a process of elimination.
Manufacturers frequently choose a familiar grade of plastic from a similar application or rely on supplier recommendations. Plastic selection is a difficult undertaking that requires several factors to be considered, including:
The type of thermoplastic resin to use for your molded product is determined by the application. For example, some plastics have high tensile strength and can survive high and low temperatures, whereas others are better at withstanding extreme temperatures.
Source: Pinterest
One of the most basic requirements in designing a part for plastic injection molding is proper wall thickness. The wall thickness of a molded object varies depending on the type of plastic resin used and the size of the part.You should make an effort to keep the wall thickness of your part as uniform as feasible. It’s fine if your walls aren’t perfectly straight, but unequal wall thickness considerably increases the chances of sink marks, warpage, voids, molded-in stress, longer cooling periods, and even material flow limits.
If the thickness of the walls must be irregular, smooth transitions that taper over time are optimal. The minimum wall thickness allowed for your plastic injection part is determined by the size of the part and the ability of the material to fill.
Many part failures can be avoided by designing your part with consistent wall thickness during the production process. When plastic melts, it flows to the weakest points in the structure. If the thickness of your part varies throughout, the melt may flow into the thick portions first (depending on gate locations). The thin portions may not fill correctly if this happens. Furthermore, thicker portions cool more slowly and are more prone to voids and sinking faults. If you design your component with rounded corners, it will be easier to fill the part properly during the molding process.
Source: Pinterest
The sharpness of each corner’s edge is measured by the radius of a plastic part. Overly sharp edges can significantly increase stress concentration, potentially leading to part failure. Sharp corners must be rounded slightly to reduce stress concentrations, which means the radius of the edge must be considered while making a molded object.
Radius should always be taken into account when calculating the thickness of a part to avoid high-stress areas and possibly part breakage. The thickness at a corner should be between 0.9 and 1.2 times the nominal thickness of the part, according to a conventional rule of thumb.
At all costs, sharp corners should be avoided. Sharp edges, like the corners of a square hole, will result in a part with a lot of molded-in stress. These frequently result in weak areas, which eventually lead to part failure and cracking. The amount of molded-in stress can be reduced by adding radii to sharp corners.Radii help to spread tension more uniformly and improves material flow and ejection from the mold. When the inside corner is less than 25% of the nominal wall thickness of the part, stresses build up quickly.
Source: Pinterest
The amount of taper on the vertical walls of the plastic item is referred to as draft. A part may not eject from the mold or maybe damaged during ejection if there is no airflow. Draft angles of 1° to 2° are often required, but they might vary based on part constraints and specifications.
Angle the vertical walls to avoid persistent contact with the molding cavity during the mold opening. All vertical walls that are normal to the mold pull direction should have a minimum draft of 1 degree. Ribs and bosses require special care, while textured surfaces require an additional 1 degree per side for each.001″ depth of roughness. A draft is an important step of the part design process.
Drafting is critical to the plastic part’s overall structure because a “vertical” draft can be harmful to the plastic item in issue, CNC machinery engineers recognize that a certain amount of draft is required when manufacturing and removing a plastic part from its mold.
Source: Pinterest
A plastic part with a thin wall thickness will not be as robust as one with a thicker wall thickness, which is why ribs may be required to aid increase the part’s strength. To eliminate sink marks, rib thickness should be between 50 and 70% of the corresponding part thickness, depending on the material. Designers may core out material to minimize fault is to avoid sinking.
Support ribs/gussets are utilized to provide additional support to a product’s walls. They’re generally employed in two situations: when a part’s walls meet at a 90-degree angle, and when a portion is excessively long or broad and the wall thickness makes it weak. Support ribs are best used in the direction in which they are required, such as along the length of a lengthy piece.
Ribs can be used to provide rigidity and stiffness to parts. Adding ribs to a part increases its strength and allows it to carry a heavier weight. Ribs have their own set of recommendations for maximizing functionality and minimizing faults.
Source: Pinterest
During the cooling process of your injection molding operation, all materials shrink at various rates and to different degrees. Two different types of shrinkage and warpage can happen. When there is a mismatch between the mold’s corresponding linear dimension and the molded part, shrinkage occurs. A dimensional distortion in a molded plastic induced by excessive residual stress is known as warpage. When attempting to regulate either of these situations, there are several factors to consider. Material considerations, component geometry considerations, tooling considerations, and processing considerations are all factors that must be considered.
The shrinkage that happens during the molding of plastic parts can be as high as 20% by volume. Thermal shrinkage is more common in crystalline and semi-crystalline materials. Amorphous materials are known to shrink less than solid solids.
Here are a few simple strategies to prevent molding shrinkage:
Source: Pinterest
Plastic pieces should be made in such a way that mold tools can simply open and expel them. The two sides of an injection mold separate in the opposite direction when a part is released. When unusual characteristics such as holes, undercuts, or shoulders inhibit the release, it may be necessary to add side actions into the design.
Working with a skilled plastic injection molder and engineering team like those in Rydtooling is essential for avoiding many of the problems that can arise during the design and development phase. You’ll be on track to get your product to market faster and on a budget if you keep these aspects in mind during the design process and work with a qualified plastics engineer.
It is dangerous to make use of components after they’ve been manufactured without encasing them with plastic. It’s essential to encase these components to make
Transparent plastic is being used in virtually every industry and this is because of its capacity to allow you see through and its ease of
Plastic is a common material used in the production of objects that can be used in homes, the automobile industry, and virtually all sectors. It
Basically, there are two kinds of plastics – thermoplastic, and thermosets. But the majorly talked about kind is the thermoplastic because of its versatile and
+86-755-8524 1121
marketing@rydtooling.com
No. 2, HongKan 1st Road, YanChuan Community, YanLuo Street, BaoAn District, ShenZhen City, China. Post Code 518105.
Subscribe to our newsletter to get manufacturing news and updates!