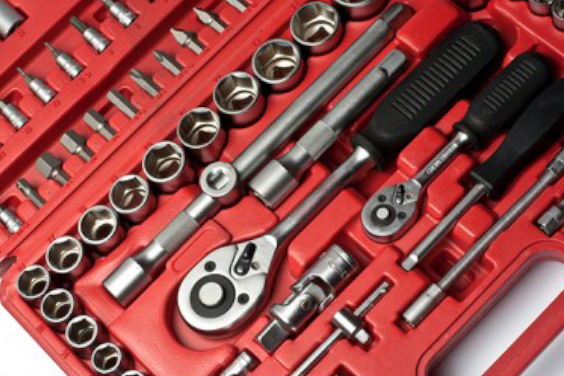
Insert Molding Process Step by Step
It is dangerous to make use of components after they’ve been manufactured without encasing them with plastic. It’s essential to encase these components to make
Share
Share
Injection molding is one of the most widespread manufacturing processes around the world. It is fast, can be used for mass production, and most of the raw materials are widely available. It is the manufacturing process that has been used to make all kinds of domestic and commercial plastic-based products that we use every day. But like any other manufacturing process, injection molding has its own challenges and issues that tend to get in the way of its efficiency.
We are going to look at the many challenges that injection molding faces, explore how to troubleshoot them successfully, and suggest some other better ways of getting around them. If you have been facing problems in your manufacturing plant, then this is for you.
There is a countless number of injection molding defects, and there’s no way of knowing that will pop up since they are triggered by so many factors. Some of these defects are old enough to ignore, but others are too severe to the point they render the product unusable. The following are some common injection molding defects, their causes, and some remedies that you can try to rectify them.
Source: www.improve-your-injection-molding.com
These are defects that appear when an injection mold is not filled up properly. This leads to the parts appearing incomplete and deformed, and it is usually serious enough to render the product as scrape. The defect tends to appear away from the gate, especially in situations where the flow distance is very long. Another common cause is thin walls and ribs that are unable to direct the molten material fast enough to the intended locations before solidifying gets the chance to begin. It is hard to miss a short shot as they are very pronounced on the final product. The following are some of the other causes of short shots.
You can counter this by making the crucible small enough to handle the injection material size and speed. You can also increase the temperatures to ensure that the molten material spreads long enough to cover the whole crate. Repair all the parts that have been damaged due to continued use, recalibrate the size of the mold to ensure it fits the needs of the batch you are working on.
Source: www.improve-your-injection-molding.com
This is a defect that is characterised by a film-like edges that appear on the molded parts near the sealing faces, venting channels, or near commissures. The defect doesn’t inflict any serious damage that can make the product unusable, but it is not a good sight to look at. There are certain causes of this condition, and they include the following.
Begin by looking at the injection pressures and calibrate them according to the needs of what you are creating. Always clean everything when starting a new batch to get rid of all contaminants in the crates and the injection nozzles. Keep an eye on the stock temperature to keep it within functional limits.
Source: Pinterest
Sink marks are depressions that appear on the surface of the molded products with varying depths depending on the thickness of the walls. Sink marks don’t really affect how the product ends up functioning unless the sink marks are too big. Most times, sink marks only affect the aesthetics of the final product, and that may be a big deal in the packaging industry. Some of the main causes of sink marks include the following.
Keep the melting temperatures as high as possible for as long as you can to ensure that there’s uniform heating which will lead to uniform cooling. You should also increase the amount of molten material to ensure it’s sufficient.
Source: www.log-imm.com
Voids are tiny bubbles and blisters which manifest themselves on molded materials and are a direct result of entrapped air being sealed into the material after cooling has taken place. It may not affect the performance of the product but in most cases, it simply impacts the appearance in a negative way, something that consumers will definitely not appreciate. The following are some of the common causes of voids in plastic molding.
To stop air from being trapped is hard, but one way of minimizing this would be to ensure the injection nozzle is clean before the injection molding begins. The process should also be unbroken to minimize the room for air to find its way into the mold. Change the design of the gate to the most appropriate location and ensure the venting is improved.
Source: www.creativemechanisms.com
Flow marks are an optical defect that is characterized by lines that appear to be following a certain pattern on the surface of the molded product. They generally appear in the area where the polymers meet to form one complement after the injection process. They also appear due to the turbulence caused by a fast injection, and they are very visible in colored molded parts. The following are some of the main causes of this condition.
Increase the injection speed to increase the uniformity. At the same time, make sure you limit the number of lubricants that you use in the process. Ensure the crate has good venting, has a properly located and constructed gate, and ensure that the temperature being used is uniform.
Source: https://live.staticflickr.com
Brittleness is a structural defect that makes the product very fragile and easy to break. This goes beyond affecting the aesthetics of the product and directly weakens the structural integrity of the final product.This manifests itself with racks and a lack of flexibility in the product. The following are the reasons why this defect occurs.
Using the right raw materials is the first step in getting rid of this defect; mixing up materials that have different melting and cooling temperatures is not advisable. Repair all the faulty parts of the crate and get the temperature to the right levels at all times.
Source: docplayer.net
Grooves are surface defects that appear across the entire product, and although they may not affect the functionality or the structural integrity of the product, they do give the product a very ugly appearance. Grooves usually appear around the point gates, spreading outwards towards the periphery. The following are some of the causes of this defect.
Getting the gate in the right palace is the first step you should take care of to ensure everything that goes in is done in the proper way through the proper channels. Maintain the stock and mold temperatures high to make sure that the molten material is able to spread out evenly, and lastly, increase the speed injection speed.
Source: www.patterson-rothwell.co.uk
Jetting is a very unique defect that is almost similar to grooves, only that it appears like a spray of molten material was sprayed across the product after it had formed. There are fine lines that appear on the surface starting from the hate going outwards covering the entire product. The pines are more pronounced in products that are darker in color and the main causes of this defect include the following.
Keep the temperature at a constant level throughout the injection process to ensure the viscosity is maintained at a level that regulates the speed of flow. The pressure should also be calibrated to match the product being made and what the crate can handle. Finally, ensure that the flow is uniform by using the right molding gates.
Source: d2n4wb9orp1vta.cloudfront.net
Air streaks appear in the form of silvery-white lines on the surface of the molded parts. They are commonly present near the ribs and domes or where the thickness of the molded parts vary. They are very hard to ignore, and they may not affect the structural integrity, but they do give the product a very undesirable appearance. The following are the common causes of this defect.
Increasing the mold temperature is a good way to counter air streaks as they are able to get rid of any moisture or air that may be entrapped in the material. Reducing the speed of injection is also another calibration that has to be taken care of. Improve the venting of the molding crate to make the product a little more perfect.
Source: www.plasticportal.eu
Color streaks are similar to air streaks, but instead of air-filled lines, these are colorful streaks that differ from the main color of the molded part. This is the unequal distribution of color during the mixing process, and once thermal integration gets into the picture, the colors get dispersed too much, and they end up creating streaks of varying colors across the surface. The following are the main causes of color streaks.
Ensure that the colors you choose to use are well balanced and well mixed. Keep the mold and stock temperatures as high as possible to ensure the material gets as much time to get into the crate and fill it evenly. You should also ensure any mechanical and structural defect in the crate is repaired beforehand. Lastly, reduce the injection pressure as that tends to disperse the colors as the molten materials are injected into the crate.
Source: Plastic Technology
Stress whitening is the white streaks that seem to appear inside the product and this is due to the combination of external and internal forces. It is very common in polymers like nylon, and it can alter the appearance and the structural integrity in a very major way. The most common places that this would appear are the de-molding points, and sometimes they can appear many days after production making it a very serious issue for consumers. The following are some of the causes of this defect.
Avoid using incompatible materials when making injection molding products since each material has its own melting and cooling points, and if this is not uniform, there’s stress build-up in the material. You should also be aware of the chemical tolerances of the materials in the molten materials before using them.
This is a distortion in the shape of the final product that usually appears many days after the process has been finished. It is caused by many factors, but the main culprit has a lot to do with heating and cooling variations. It tends to appear in large and flat objects, and the following are the common causes of the defect.
Keeping the temperatures of the stock and mold at a high level will help in spreading some uniformity across the board. Freeing the gate during the injection process will also get rid of the backlog, and this will lead to a free and unrestricted flow of molten material to the needed parts. You should also ensure that every part of it is well designed for the functions.
Source: www.miconmould.com
Burnet Streaks are one of the most common defects that mostly affect the appearance. They frequently occur due to the fact that the entire process relies on heat, and the chances of some parts coming out scorched a little are high. These burnt streaks manifest in the form of brownish and silver discolorations on some particular parts of the molded article. The following are the causes of this defect.
Source: https://i.redd.it
Mold sticking is the process where the molded part cannot be ejected properly due to some parts being stuck to the crate. This occurs when the lubrication is not sufficient enough to allow the molded plastic to detach itself after the cooling has taken place. This can have the very undesirable effect of deforming the product to the point where it cannot be used. The following are the main causes of this defect.
When handling the infection process, make sure you only infect the needed amount. Filling the crate overcapacity will affect the cooling process, and the likelihood of sticking on some parts of the mold increases. You should use proper and sufficient lubrication to make work easier for the ejector. And finally, ensure that you don’t undercut any part of the process, be it the machinery or the material.
Injection molding is clearly a process that is not without any issues. The best molding manufacturers are those that are able to work around these defects and still produce top-quality products that meet the safety standard for consumers. If you are interested to know more about injection molding, other defects that exist, and what you can improvise to make things better, then check out our website and have all your questions answered by a team of experts.
It is dangerous to make use of components after they’ve been manufactured without encasing them with plastic. It’s essential to encase these components to make
Transparent plastic is being used in virtually every industry and this is because of its capacity to allow you see through and its ease of
Plastic is a common material used in the production of objects that can be used in homes, the automobile industry, and virtually all sectors. It
Basically, there are two kinds of plastics – thermoplastic, and thermosets. But the majorly talked about kind is the thermoplastic because of its versatile and
+86-755-8524 1121
marketing@rydtooling.com
No. 2, HongKan 1st Road, YanChuan Community, YanLuo Street, BaoAn District, ShenZhen City, China. Post Code 518105.
Subscribe to our newsletter to get manufacturing news and updates!